大家好!今天让小编来大家介绍下关于铝合金薄壁零件(铝合金薄壁零件加工)的问题,以下是小编对此问题的归纳整理,让我们一起来看看吧。
文章目录列表:
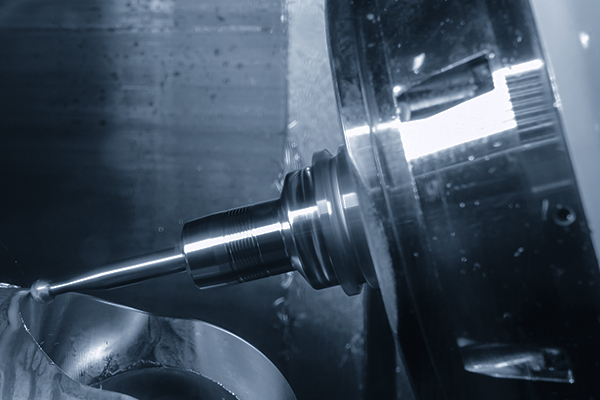
在压铸中 壁厚小于多少的算是薄壁件
这个可能没有统一的标准答案,现在的压铸机性能越来越好,压铸
技术也越来越先进,所以可以生产的压铸件的产品的壁厚也越来越薄,而且,铸件面积的不同,可生产的最小壁厚也会不同。按以前的经验,铸件的面积在25cm²以下时,锌合金可以生产0.5mm的零件,铝合金、镁合金、铜合金可以生产出0.8mm的铸件。对于面积大于25~100cm²的铸件,锌合金可以生产1.0mm的壁厚零件,铝合金、镁合金可以生产1.2mm壁厚的零件,铜合金可以生产1.5mm壁厚的零件。对于面积在100~500cm²的铸件,锌合金可以生产1.5mm的壁厚零件,铝合金、镁合金可以生产1.8mm壁厚的零件,铜合金可以生产2.0mm壁厚的零件。对于面积大于500cm²的铸件,锌合金可以生产2.0mm的壁厚零件,铝合金、镁合金可以生产2.5mm壁厚的零件,铜合金可以生产2.5mm壁厚的零件。但现在这个记录可能已经刷新了。以上仅作参考。
浇铸铝合金的性能怎样?压铸铝合金的性能怎样?两者那一种更好一些?谢谢
浇注铝合金在强度上比压铸的要高,但表面的质量较压铸的差,尺寸也比较粗,压铸的尺寸复杂程度,表面质量都较好,但是强度较低,零件的内部组织较酥松。
五坐标数控机床,加工深腔、薄壁零件。铝合金材料。如何解决颤纹?
楼主的意思我基本明白。铝合金件,中间掏个腔体,而且周围壁厚较薄。
有的东西本身就是比较难加工的,对于这些问题没有谁说能给予完全的解决,只能说相对效果好一些。
我理解,振纹应该主要出现在侧面,这个是正常的。因没有具体图纸等,下面我泛泛的提供2条解决方案:
1、粗加工时使用你们平时的刀具就可以了,在走最后一刀的时候,换成那种刀具刃口总长度较短的刀具(希望你能理解我的话),(侧面振纹多半跟切屑的总深度过深有一定关系。)然后分段依次加工完成。
2、有一种刀具可以改变主轴的方向,就是主轴本身是垂直方向的,接一个工具让他改成水平方向,然后按上直径较小的盘铣刀,铣加工侧面。就是把铣刀掰90度加工。
薄壁铝合金件,由于铝件的质地较软,容易让刀,容易造成宽度尺寸不准,根据床子的能力和具体的壁厚,尽可能提高转速和减小切屑余量。。。
侃侃而谈,希望对你有帮助。
另外,你说的支撑零件的方法,我认为不太可取,支撑泄掉之后,尺寸就完全不对头了。
铝件加工既然这么容易变形,就没有好办法了吗
在飞机结构中,为了减轻重量,采用了大量的铝合金材料的薄壁零件,由于铝合金零件材料热膨胀系数较大,薄壁加工过程中很容易变形。尤其是在采用自由锻毛坯时,加工余量大,变形问题更为突出。
铝合金零件加工变形的原因很多,与材质、零件形状、生产条件、切削液的性能等都有关系。
引起变形的原因,主要有以下几个方面:
毛坯内应力引起的变形
切削力引起的变形
切削热引起的变形
夹紧力引起的变形
所以,在加工过程中,减少加工变形的措施就尤为重要。
工业措施
减少加工变形的措施,主要有以下几个方面:
降低毛坯的内应力
改善刀具的切削能力
合理选择刀具几何参数
改善刀具结构
改善工件的夹装方法
合理安排工序
降低毛坯的内应力 采用自然或人工时效以及振动处理,均可部分消除毛坯的内应力。预先加工也是行之有效的工艺方法。对肥头大耳的毛坯,由于余量大,故加工后变形也大。若预先加工掉毛坯的多余部分,缩小各部分的余量,不仅可以减少以后工序的加工变形,而且预先加工后放置一段时间,还可以释放一部分内应力。
改善刀具的切削能力 刀具的材料、几何参数对切削力、切削热有重要的影响,正确选择刀具,对减少零件加工变形至关重要。
(1)合理选择刀具几何参数。
①前角:在保持刀刃强度的条件下,前角适当选择大一些,一方面可以磨出锋利的刃口,另外可以减少切削变形,使排屑顺利,进而降低切削力和切削温度。切忌使用负前角刀具。
②后角:后角大小对后刀面磨损及加工表面质量有直接的影响。切削厚度是选择后角的重要条件。粗铣时,由于进给量大,切削负荷重,发热量大,要求刀具散热条件好,因此,后角应选择小一些。精铣时,要求刃口锋利,减轻后刀面与加工表面的摩擦,减小弹性变形,因此,后角应选择大一些。
③螺旋角:为使铣削平稳,降低铣削力,螺旋角应尽可能选择大一些。
④主偏角:适当减小主偏角可以改善散热条件,使加工区的平均温度下降。
(2)改善刀具结构。
①减少铣刀齿数,加大容屑空间。由于铝件材料塑性较大,加工中切削变形较大,需要较大的容屑空间,因此容屑槽底半径应该较大、铣刀齿数较少为好。
②精磨刀齿。刀齿切削刃部的粗糙度值要小于Ra=0.4um。在使用新刀之前,应该用细油石在刀齿前、后面轻轻磨几下,以消除刃磨刀齿时残留的毛刺及轻微的锯齿纹。这样,不但可以降低切削热而且切削变形也比较小。
③严格控制刀具的磨损标准。刀具磨损后,工件表面粗糙度值增加,切削温度上升,工件变形随之增加。因此,除选用耐磨性好的刀具材料外,刀具磨损标准不应该大于0.2mm,否则容易产生积屑瘤。切削时,工件的温度一般不要超过100℃,以防止变形。
改善工件的夹装方法 对于刚性较差的薄壁铝件工件,可以采用以下的夹装方法,以减少变形:
①对于薄壁衬套类零件,如果用三爪自定心卡盘或弹簧夹头从径向夹紧,加工后一旦松开,工件必然发生变形。此时,应该利用刚性较好的轴向端面压紧的方法。以零件内孔定位,自制一个带螺纹的穿心轴,套入零件的内孔,其上用一个盖板压紧端面再用螺帽背紧。加工外圆时就可避免夹紧变形,从而得到满意的加工精度。
②对薄壁薄板工件进行加工时,最好选用真空吸盘,以获得分布均匀的夹紧力,再以较小的切削用量来加工,可以很好地防止工件变形。
另外,还可以使用填塞法。为增加薄壁工件的工艺刚性,可在工件内部填充介质,以减少装夹和切削过程中工件达变形。例如,向工件内灌入含3%~6%硝酸钾的尿素熔融物,加工以后,将工件浸入水或酒精中,就可以将该填充物溶解倒出。
合理安排工序 高速切削时,由于加工余量大以及断续切削,因此铣削过程往往产生振动,影响加工精度和表面粗糙度。所以,数控高速切削加工工艺过程一般可分为:粗加工-半精加工-清角加工-精加工等工序。对于精度要求高的零件,有时需要进行二次半精加工,然后再进行精加工。粗加工之后,零件可以自然冷却,消除粗加工产生的内应力,减小变形。粗加工之后留下的余量应大于变形量,一般为1~2mm。精加工时,零件精加工表面要保持均匀的加工余量,一般以0.2~0.5mm为宜,使刀具在加工过程中处于平稳的状态,可以大大减少切削变形,获得良好的表面加工质量,保证产品的精度。
操作技巧
铝件材料的零件在加工过程中变形,除了上述的原因之外,在实际操作中,操作方法也是非常重要的。
对于加工余量大的零件 为使其在加工过程中有比较好的散热条件,避免热量集中,加工时,宜采用对称加工。如有一块90mm厚的板料需要加工到60mm,若铣好一面后立即铣削另一面,一次加工到最后尺寸,则平面度达5mm;若采用反复进刀对称加工,每一面分两次加工到最后尺寸,可保证平面度达到0.3mm。
板材零件上有多个型腔,加工时,不宜采用一个型腔一个型腔的次序加工方法,这样容易造成零件受力不均匀而产生变形。采用分层多次加工,每一层尽量同时加工到所有的型腔,然后再加工下一个层次,使零件均匀受力,减小变形。
通过改变切削用量来减少切削力、切削热。在切削用量的三要素中,背吃刀量对切削力的影响很大。如果加工余量太大,一次走刀的切削力太大,不仅会使零件变形,而且还会影响机床主轴刚性、降低刀具的耐用度。如果减少背吃刀量,又会使生产效率大打折扣。不过,在数控加工中都是高速铣削,可以克服这一难题。在减少背吃刀量的同时,只要相应地增大进给,提高机床的转速,就可以降低切削力,同时保证加工效率。
走刀顺序也要讲究粗加工强调的是提高加工效率,追求单位时间内的切除率,一般可采用逆铣。即以最快的速度、最短的时间切除毛坯表面的多余材料,基本形成精加工所要求的几何轮廓。而精加工所强调的是高精度高质量,宜采用顺铣。因为顺铣时刀齿的切削厚度从最大逐渐递减至零,加工硬化程度大为减轻,同时减轻零件的变形程度。
压紧件的问题薄壁工件在加工时由于装夹产生变形,即使精加工也是难以避免的。为使工件变形减小到最低限度,可以在精加工即将达到最后尺寸之前,把压紧件松一下,使工件自由恢复到原状,然后再轻微压紧,以刚能夹住工件为准(完全凭手感),这样可以获得理想的加工效果。总之,夹紧力的作用点最好在支承面上,夹紧力应作用在工件刚性好的方向,在保证工件不松动的前提下,夹紧力越小越好。
在加工带型腔零件时加工型腔时尽量不要让铣刀像钻头似的直接向下扎入零件,导致铣刀容屑空间不够,排屑不顺畅,造成零件过热、膨胀以及崩刀、断刀等不利现象。要先用与铣刀同尺寸或大一号的钻头钻下刀孔,再用铣刀铣削。或者,可以用CAM软件生产螺旋下刀程序。
工件变黑
铝是活泼金属,在一定的温度和湿度条件下极易氧化变黑或发霉,这是铝本身的特性决定的,选用的清洗剂具有强腐蚀性,造成压铸铝腐蚀氧化。
铝合金工件的变形问题和解决方法是什么?
铝合金是工业中使用最广泛的一类有色金属结构材料,在航空、航天、汽车、机械制造、船舶及化学工业中均有铝合金工件。在飞机结构中为了减轻重量,采用了大量的铝合金材料的薄壁零件,由于铝合金零件材料热膨胀系数较大,薄壁加工过程中很容易变形。尤其是在采用自由锻毛坯时余量大,变形问题更为突出。
一、铝合金工件切削变形的原因
铝合金零件变形的原因很多,与材质、零件形状、工艺条件、切削油的性能等都有关系。主要有以下几个方面:毛坯内应力引起的变形,切削力、切削热引起的变形,夹紧力引起的变形。
二、减少工件变形的工艺措施
(1)降低毛坯的内应力
采用时效以及振动处理或预先工艺均可部分消除毛坯的内应力,余量大的毛坯工件故变形也大。若预先去掉毛坯的多余部分缩小各部分的余量,不仅可以减少以后工序的变形,而且放置一段时间,还可以释放一部分内应力。
(2)合理选择刀具几何参数
前角:在保持刀刃强度的条件下前角适当选择大一些,一方面可以磨出锋利的刃口,另外可以减少切削变形使排屑顺利,进而降低切削力和切削温度。
后角:后角大小对后刀面磨损及表面质量有直接的影响。粗铣时由于进给量大、切削负荷重、发热量大,要求刀具散热条件好,因此后角应选择小一些。精铣时要求刃口锋利,减轻后刀面与表面的摩擦减小弹性变形,因此后角应选择大一些。
螺旋角:为使铣削平稳降低铣削力,螺旋角应尽可能选择大一些。
主偏角:适当减小主偏角可以改善散热条件,使平均温度下降。
(3)改善刀具结构
减少铣刀齿数加大容屑空间。由于铝合金材料塑性较大切削变形较大,需要较大的容屑空间,因此容屑槽底半径应该较大、铣刀齿数较少为好。
(4)精磨刀齿
在使用新刀之前,应该用细油石在刀齿前、后面轻轻磨几下,以消除刃磨刀齿时残留的毛刺及轻微的锯齿纹。这样不但可以降低切削热而且切削变形也比较小。
(5)严格控制刀具的磨损标准
刀具磨损后工件表面粗糙度值增加,切削温度上升工件变形随之增加。因此除选用耐磨性好的刀具材料外,还应严格控制刀具磨损程度,否则容易产生积屑瘤。切削时工件的温度不能过高以防止变形。
(6)改善工件的夹装方法
对于刚性较差的薄壁铝合金工件,对于薄壁衬套类零件如果用三爪自定心卡盘或弹簧夹头从径向夹紧,一旦松开工件必然发生变形。以零件内孔定位自制一个带螺纹的穿心轴套入零件的内孔,其上用一个盖板压紧端面再用螺帽背紧。外圆就可避免夹紧变形从而得到满意的精度。
(7)切削油的选用
由于铝合金的硬度较低且切削性较差,对切削油的冷却、润滑、渗透及清洗性能有更高的要求,另外还需要一定的抗腐蚀性能以防止工件发黑,常用的切削油切削过程中能在金属表面形成高熔点硫化物,而且在高温下不易破坏,具有良好的润滑作用,并有一定的冷却效果,一般用于切削、钻孔、铰孔及攻丝等工艺。
以上就是小编对于铝合金薄壁零件(铝合金薄壁零件加工)问题和相关问题的解答了,铝合金薄壁零件(铝合金薄壁零件加工)的问题希望对你有用!